
The Energy Challenge 2004 - Solar
11.11.04
Murray Duffin, Retired
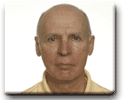
Solar energy is our most abundant renewable resource.
An analysis of insolation in the USA southwest shows
that using only the 1% of the land area considered,
that has a slope of <1% and >7kWh/sq. m./day
insolation, concentrated solar (CSP) can provide power
of approximately 30 Gwe. With effective storage (as
for solar towers) this potential could provide at
least 3x the total productive energy of today's economy.
Solar energy generation can be considered in 3 categories,
solar thermal, solar photovoltaic (PV), and solar
thermophotovoltaic (TPV). As TPV is still a far future
technology, only the first two will be considered
here. 2004 may have been the watershed year for the
development of solar renewable energy, although that
may not become obvious for several more years. While
there has been little progress in installations in
some years, technology has continued to improve, and
with rising costs of coal oil and natural gas, interest
in solar energy is now growing rapidly.
The new economic driver
North American production of natural gas is reported
to have declined by more than 3% in 2003 vs. 2002,
and based on reports by the major producers in America,
production in 2004 seems to have declined at least
3% in the first half, and as much as 10 to 12% in
the third quarter y-o-y. Hurricane damage can account
for less than 40% of Q3 decline, so it seems that
decline of mature fields is accelerating. Against
earlier forecasts of natural gas prices below $5.00/Mbtu
for H2 2004, recent cash prices have been above $7.00,
at a time when demand is low, and storage is at record
levels.
At the same time export demand for coal has caused
prices to more than double, on average, for all but
Powder River Basin coal; and we have seen oil prices
rise 70% in a few months and are going into winter
with heating oil stocks low and prices high. With
possible brief respites, these trends appear irreversible.
Solar Thermal Overview
There are 2 major sets of solar thermal:
Direct heating and cooling
Electricity generation.
Each can be split into flat plate and concentrating
(CSP) subsets although for electricity generation
CSP is the economic choice for all but small-scale
applications.
- Direct heating and cooling
The mature technology is water heating for home
hot water, space heating and swimming pool heating.
Flat plate technology is common, inexpensive and
effective and has been used successfully with gradual
growth for at least 50 years. Efficiency can be
in the 25 to 50% range, depending on design. More
recent technology that is growing rapidly, and is
the preferred choice for larger installations like
hotels and public swimming pools is evacuated tube
heating systems which provide much more heat per
unit area, remain effective even during light overcasts,
and can reach 60% conversion efficiency.
Recently compound parabolic concentrators (CPC)
have begun to be industrialized, proving very
effective in evacuated tube systems. The advantage
of CPC is that, by concentrating sunlight it can
raise liquid temperature in pressurized systems
to >300 degrees F, enabling economic absorption
chillers for cooling systems. CPC is also effective
over a very wide angle of illumination, eliminating
the need for a tracker in a concentrator system.
The California Energy Commission retrofitted and
optimized a 20 ton conventional double effect
(2E) LiBr/water absorption chiller to be solar
hot water driven, and have estimated that such
a system can be supplied commercially for <$4500./ton,
with a net reduction in electricity demand of
1.3kW/ton. Depending on hours/yr of operation
and peak electricity costs, an economic payback
of 4 to 8 years can be expected.
Direct heating and cooling systems have the
effect of displacing electricity, to use Amory
Lovinss term, providing "negawatts"
instead of megawatts, and generally at lower cost
than increased generating capacity.
- Electricity generation (CSP)
Thermal power generation is being addressed
in several ways—and for different sizes
of installation:
- Solar dish concentrators driving Sterling
engine generators.
- Trough concentrators heating a liquid to
gas system driving a turbine generator.
- Solar towers using large reflector (heliostat)
arrays to heat molten salts which, through a
heat exchanger, drive steam turbines.
- Solar chimneys using rising air from a large
ground level greenhouse to drive turbines at
the base of a km high chimney.
CSP Details
Dish/Sterling systems tend to be aimed at tens of
kW applications for grid connected distributed power,
and reach conversion efficiencies near 30%. Cost of
electricity is still high, though there is a wide
range of estimates. Widespread use seems likely to
be well in the future.
Trough concentrators get into the 100s of kW to
tens of MW range, good for locally sighted factory
power also at attractive efficiencies. The best-known
examples are the SEGS series (now up to SEGS 9) in
California. Recent projects have been commissioned
in Nevada and Arizona. It has been estimated that
a 100 mi. square in the Nevada desert could provide
about 500 GWe, roughly equal to the USA installed
electric power base. Up to now such applications have
limited storage ability, so they are unsuitable to
24 hr. operation and dispatched power. CPC concentrators
might overcome that drawback. These systems approach
14% efficiency today and are projected to get to 17%
by about 2015.
Solar towers (Power Towers) are MW sized for utility
type supply and have the advantage of retaining heat
for 24-hour operation. Solar 1 was operated near Barstow
Ca. in the 1980s as proof of concept. Solar 2, a 10
MWe upgrade of Solar 1 operated from 1992 to 1999,
demonstrating the feasibility of storing heat for
dispatchable power and 24 hr. operation. Solar Tres
(17 MWe) has been planned for Spain, originally to
go into operation by late 2003, but now delayed to
2006, seemingly by bureaucracy. Towers in the 100
MW range are projected. Solar towers are about 23%
efficient in conversion of incident energy to electricity,
and can realize up to 70% capacity factor. Current
experience indicates a space demand of 10 acres/MW,
with promise of at least a 20% reduction.
Solar chimneys4,5 are only theoretical
so far, and seem to have captured most attention in
Australia. They can be designed to heat water during
the day to provide energy at night. Efficiency is
estimated as 3%, but it seems likely that this can
be at least doubled. Proposed designs have fresh air
drawn into the heating area at ground level. Drawing
in air near the tower top would augment generation
with the sinking column of cooler air. In dry climates
it should be possible to inject water vapor into intake
air to further cool the descending air column. Current
projected design is for 200 MW and requires about
23 acres/MW. Capital cost of $2.00/Wp is projected,
but seems quite optimistic.
For utility scale electricity generation, the best
choices today are trough concentrator and solar tower
systems. An excellent 2003 analysis for trough concentrators2
(based on 2002 data and projections) considers a necessary
competitive target price for electricity of $4.50/MBtu,
assuming a floor fixed at that level by LNG. We now
can be sure that LNG will not be a major factor for
at least a decade, and even then will set a floor
above $6.00/Mbtu. This analysis showed trough systems
becoming competitive at 10 Gwe installed capacity
and 6 cents/kWh. It now seems more likely that 7-8
cents/kWh will be good which can be reached at 5-6
Gwe installed. Another late 2003 report3,
using well reviewed data and analysis developed independently
be Sunlab and Sargent & Lundy gives present electricity
costs of 10 – 12.6 cents/kWh now, going to 3.5-5.5
cents/kWh before 2020 for trough and tower systems.
Growing fossil fuel shortages seem certain to accelerate
progress relative to these studies.
Photovoltaic (PV)
Historically PV has been seen as much too expensive
for widespread use, having been represented as "the
energy of the future and always will be". 2003
saw a novel development that should change that conclusion.
All of the pieces now seem to be in place for PV to
breakthrough all the barriers of demand, cost and
capacity that have been holding it back, but it seems
that no one in the North American PV or electric utility
industries has seen all the pieces yet, let alone
put them together to make a picture
Recent NG demand growth is largely for electricity
generation. From 1993 through 2003 nearly 300 GW of
electrical generating capacity was installed in the
USA, about 90% of which is NG fired, both to meet
Clean Air Act requirements, and to add flexible capability
to meet peak loads. Base load demand is estimated
to grow at least 1.5%/yr (6 GW/yr), but seems to have
shot up by at least 5% in 2004 vs. 2003. Therefore
NG fired supply, intended for peaking, is being converted
to base load supply, leaving a growing shortage of
peaking capacity. Now declining NG supply means that
peaking demand growth can no longer be met by adding
new NG fired capacity. However peak demand coincides
with peak insolation making PV an attractive alternative.
So, we have demand, at least if the cost is not
too high. Can needed costs be met, and can there be
adequate supply? In Renewable Energy World, Dec 2002,
Auliche and Schulze (A&S) estimated worldwide
polysilicon feedstock capacity for electronic grade
(EG) silicon at 26,000 metric tons (MT)/yr, with production
estimated at 14,000 MT/yr. With such a large excess
capacity, poly suppliers have been happy to sell EG
silicon for PV production at very attractive prices
($20.00-25.00/kg), enabling PV producers to lower
their prices. As Maycock noted in Solar Today, Jan/Feb
2004, PV producers have sold cells and modules at
cost, enabling very rapid industry growth in 2001-2003.
System quotes as low as $4.00/Wp installed have been
mentioned. Total world Si PV production in 2003 was
about 0.7 GWp, having grown 32% worldwide while
actually shrinking in the USA.
A&S estimated that about 2000 MT each of "off
spec" and "non-prime" EG Si were supplied
to the PV industry in 2000. At 17 MT/MWp that was
enough to produce 235 MWp in 2000. Maycock shows 2000
production at 288 MWp, which implies another 1000
MT from capacity dedicated specifically for PV. With
perhaps 8000 MT excess capacity in 2000 suppliers
have had no incentive to add capacity. However, production
of >700MWp in 2003 has surely consumed the excess
capacity, even if price may not yet have been attractive
for the poly producers. In parallel, while technology
is reducing the share of off spec and non-prime Si
being produced, microelectronics demand for Si is
growing rapidly. As a result, in the last 12 months
the price of poly has gone from $20.00-25.00/kg to
>$30./kg and is projected to go to $40.00-60.00/kg.
These price increases push bottom prices for PV installations
back to the range of $6.00-7.00/Wp.
While there may still have been some stockpiles
from prior years to work off in 2004, it is probably
safe to say that PV growth will now be limited by
poly capacity and price. To aggravate the situation,
during the 2000-2003 period, poly producers experienced
very low ROI, making it difficult now to attract the
large increments of capital needed for conventional
“Siemens process” poly production capacity.
Unless there are dramatic technical advances, this
condition is likely to persist for several years.
John Schumacher has pointed out (Solar Today, Jan/Feb
2004), that breakthroughs are needed in both poly
capacity capital and production costs, and in ways
to get more collector surface per ton of poly. Fortunately,
it seems that the technology now exists to meet both
needs, and the only delay factor is time to recognition
and industrialization.
Schumacher7 has already operated a "proof
of concept" facility for a new poly process that
has a capital cost about 40% of that for the Siemens
process and projected product price of <$15.00/kg.
Existing, possibly surplus, CZ pullers can be adapted
to use the output of this new process with a probable
increase in throughput at lower energy input, further
lowering the cost of PV wafers.
In Dec. 2003, Origin Energy of Australia8,
in conjunction with the Australian National University
(ANU) announced a new "sliver cell"6
approach to making PV cells from Si wafers that is
a classic example of "lateral thinking".
Origin claims a 12x increase in collector surface
per ton of silicon, and a 30x potential increase in
Wp/wafer. My calculations do not confirm these claims,
but taking all yield factors into account, they can
probably get to >6x increase in collector surface/ton,
which is still a sufficient breakthrough.
In 2004 ANU delivered a paper6 on sliver
cells in concentrator applications, showing a 21%
conversion efficiency at 20 suns. The Fraunhofer Institute
has also worked with very thin silicon for PV and
show 24% efficiency at 60 suns. Even at 20 suns and
6x yield/ton, poly scarcity ceases to be a restraint.
In writing a National Energy Policy “primer”
for the House and Senate Energy Committees in 2001
(which regrettably, but not surprisingly, they totally
ignored), I estimated that we would need the output
of 50 large factories for 20 years to install enough
collector surface at 20 suns to produce 10 quads of
PV solar energy per year. The sliver cell will enable
5 quads in 20 years with only 4 factories. What seemed
quite impractical in 2001, now appears quite feasible.
Sliver Cell Whole System Pluses
. ANU notes that the cells can readily be connected
in series, reducing the need for protective diodes
and eliminating the transformer from the inverter.
In addition to lowering system cost, these changes
would also improve conversion efficiency to a-c significantly,
thus reducing the needed collector area for a given
Wp. Taking all of these factors into account (Schumacher's
poly + 6x surface increase/MT + elimination of diodes
and transformer + light weight deriving from thin
slivers + system efficiency) it seems likely that
PV could get to an installed cost of $1.50/Wp before
2010. (ANU has estimated $1.80/Wp, but it’s
not clear that they took all factors into account).
In a concentrator system, when used for peaking
power in conjunction with a CCGT, the concentrator
could also preheat water for the steam turbine stage,
potentially increasing CCGT output by at least 3%,
at no additional cost. If a 500 MW CCGT installation
needed 100 MW for peaking, the extra 15 MW of thermal
energy would lower the total investment per effective
Wp to about $1.30. With regulated utility type financing
(cost of money 3% above inflation) the resulting peaking
electricity could be provided at a cost near 13 cents/kWh.
Historic PV electricity cost estimates have typically
been quoted (see the Wall Street Journal Special Report
Sept. 2001) as 22 to 40 cents per kWh.
The average retail price of electricity in the USA
in 2002 was 7 cents/kWh, and is surely higher now.
Peak electricity price can be at least 3x, making
conventional PV historically uncompetitive. (In some
Calif. districts, base rates are 12 cents/kWh and
conventional PV is marginally competitive for peak
power now). At a base cost of 13 cents/kWh, even after
markup for maintenance and OH, PV would be attractive
for peaking supply across the southern tier. This
base cost leaves room for attractive profit margins
for everyone. I would expect NG fired power suppliers
to start pushing very hard to have these technologies
industrialized as rapidly as possible.
Conclusions
Solar thermal energy for hot water has long been
attractive, and recent developments now make it attractive
for air conditioning as well. Widespread use could
reduce electricity demand in the USA by at least 10%,
and this degree of reduction will probably become
necessary as NG supply declines.
CSP for electricity production begins to look attractive
with rising cost of fossil fuels and very long permitting
and construction times for nuclear. The technology
is now well-understood and poised for rapid development
with corresponding cost reductions. We now need an
intelligent National Energy Policy (NEP), with relatively
modest subsidies to kick-start the needed development.
We can be very confident of successful exploitation.
A major breakthrough in PV technology has now raised
the potential of PV to the level of practicality.
Production capacity is still a limiting factor. Lack
of awareness is also a barrier. Again, an intelligent
NEP is the key to further progress.
Reliance on imported fossil fuel energy, with its
attendant cost, security risk and negative payments
balance could realistically be overcome in less than
20 years, with a government driven “Apollo Program”
for energy, focused on efficiency, conservation, renewables
and nuclear. Renewable solar energy is now positioned
to make its contribution.
References:
1) http://www.energylan.sandia.gov/sunlab
2) http://www.eere.energy.gov/solar/pdfs/3solar_henryprice.pdf
3) http://www.energylan.sandia.gov/sunlab/PDFs/Assessment.pdf
4) http://www.sbp.de/de/html/projects/solar/aufwind/pages_auf/principl.htm
5) http://www.visionengineer.com/env/solar_flue2.shtml
6) http://solar.anu.edu.au/pages/publications2004.html
7) http://jcschumacher.com/
8) http://www.originenergy.com.au/news/news_detail.php?newsid=233&pageid=82
Readers Comments
Date |
Comment |
Roger Arnold
11.12.04 |
Great article,
Murray, with lots of specific numbers. That's
always nice. Good references too.
I'm a little dubious about some of the statements
about modules based on the sliver cell technology.
While I certainly agree that it's a very promising
technology for delivering much higher PV surface
area per wafer, I don't understand why it should
be any different from conventional PV in terms
of module voltage or need for diode protection
from shading. Conventional solar cells can be
and normally are connected in series. Modules
normally deliver a much higher voltage than
the individual cells. Actually, I think they're
connected in series-parallel networks that minimize
shading losses. Isn't it the series connection
that gives rise to the need for bypass diodes
in the first place?
I also doubt that a higher module voltage
would make much difference in the cost or efficiency
of the inverter. Inverters are dominated by
the cost of power switching silicon. Inductors
and capacitors are comparatively minor components.
(At least, that's my impression. I'm certainly
no expert in that area.) It's true, though,
that power switches are most efficient when
switching a few hundred volts--the "sweet spot"
for IGBT operation. And a few hundred volts
is higher than conventional modules are wired
to produce. But 48 volts is common, and I've
never heard anybody complain that inverters
driven from 48 volts lose much efficiency from
too low an input voltage. They don't use transformers,
BTW, to get 110 V on the AC outlet. I'm pretty
sure that all modern high power inverters are
formally switching DC - DC power supplies in
buck-boost configurations. The "DC" output level
is simply varied from +110V to -110V at 60 cycles
per second.
Finally, I'm very doubtful of the suggestion
that waste heat from concentrator modules could
be used to pre-heat boiler water and improve
the efficiency of a CCGT's steam turbine by
3%. High temperatures at the silicon junction
badly degrade the performance of PV cells. For
maximum efficiency from the PV system, you want
the junctions cooled as closely as possible
to ambient.
Though here's a thought: maybe one could use
photonic array methods to give the concentrator
two distinct focal distances: one for those
near IR wavelengths most efficiently converted
by silicon PV junctions, and another for all
other wavelengths. Then it might be possible
to have both a cool PV junction and a solar-thermal
heat source. Wonder if that would work ...
One thing we most definitely agree on, however,
is that the U.S. PV industry is being short-sighted
in sticking with conventional silicon PV cells
built from off-spec EG silicon. That's a recipe
for no progress. Are they taking lessons from
NASA?
|
Len Gould
11.12.04 |
Murray: Another excellent article. I hadn't
heard of sliver solar before. Surprising how
similar it is to spheral solar's approach http://www.spheralsolar.com/2_spheral-technology/2_manufacturing-process.asp
(Subsidiary of ATS Automation) They've just
opened a new manufacturing facility in Cambridge,
Ontario. Has been very hard to get performance
data on their products, though. If performance
is anywhere reasonable, however, I'd guess their
automation capabilities and the greater ease
of automating the process should give them an
edge. Interesting to follow.
If a person had to bet on which generation
system will be cheapest (capital / peak kw at
useful time) 25 years from now, it looks very
risky to bet against solar PV with it's recently
sustained record of 18%/yr cost reductions.
|
Todd McKissick
11.15.04 |
Murray: Nice article. I consider myself somewhat
knowledgeable on this subject and still gained
a substantial new understanding in some areas.
Thanks for putting in the effort. I have some
comments however.... Given CSP prices going
from 10-12.6 cents/kWh now to 3.5-5.5 cents/kWh
by 2020 and PV prices going from 22-40 cents/kW
in 2001 to 13 cents/kW sometime(?)... Given
that PV is very sensitive to Si availability
and production limitations... Given that major
technological advances in PV still only result
in minor efficiency or production gains when
CSP grows from a current 20+%... why is PV constantly
over-promoted while CSP is only admitted that
it "can" be viable? I notice that each of the
4 types of solar thermal received one paragraph
of detail on them while PV development received
12. Research was quoted in numerous PV processes,
giving details of advancements both past and
future. Material availability, justifications
for both cost and capacity, and many other details
were mentioned. I must say that given the quality
of your past articles and the level of detail
given here for PV, I'm very disappointed in
your investigation of the other solar options.
In my view, when apples are compared to apples,
solar thermal beats all other options in short
and long term as well as installed and running
costs. (I can't remember where I saw it, but
Solar II was supposedly cost competitive a decade
ago) I am not totally surprised by your assessment
since you are simply following suit of every
other organization on the net. This, I believe,
is the exact problem. Solar thermal research
seems to be the stepchild of the US government.
It is the only RE source that has no private
sector research going on. Basically, the government
has deemed it only viable on a very large scale
and everyone believes them. This has eliminated
all grants in this area as well as scared off
the private investment community. This has in
turn stagnated the private sector development
making it a self fulfilling prophecy. I would
have liked to see you trade some print for this
issue from maybe the issue of whether or not
a new PV process can eliminate its diodes. Possibly
the issue of using PVs excess heat to preheat
boiler water could have been left out as well
since that is already done by the exhaust of
the boiler to get boilers' efficiency where
it is today. It also seems unfair to justify
PVs costs by pitting them directly against today's
(over) 7 cents/kWh rate and its sometimes 12
cents/kWh rate, when CSP is only stated as becoming
economic below 7-8 cents/kWh. Lastly, the potentially
strongest point for CSP, which was only glazed
over, is the fact that CSP is not only capable
of 100% capacity with correctly implemented
thermal storage but also 100% dispatchable.
CSP also has the added capability of easily
supplementing that thermal storage with bio/fossil
fuels for emergency/critical backup. Make no
mistake, I fully support the PV effort and applaud
your diligence on that topic. However, in light
of these issues, I would like to see comments
on the limited focus of both private and public
on solar thermal technologies. I have to wonder
where it would be if it had one-tenth the research
budget that PV gets.
|
Murray Duffin
11.15.04 |
Roger - If you quantify your doubts, I would
welcome the resulting analysis. You'll probably
end up with a number between 1.3 and 1.8 $/Wp
and still have an attractive result. Len - I
have also followed Spheral, but do not find
technical analyses, and can't see how it can
come close to sliver cells for reduced Si. Sliver
cells can be 60 microns thick. I don't believe
there is any automation technology to handle
60 micron Dia. spheres. Todd - I put more words
on PV because this new breakthrough really changes
the picture. I agree with you that thermal CSP
has a larger role to play, but that is already
well accepted, especially for base load. The
real PV peaking potential needs to be understood
also. Have you considered providing a paper
on thermal? Murray
|
Len Gould
11.16.04 |
Murray: While
you may be right about Spheral Solar's Si usage,
there are other factors. According to a Netherlands
study, http://www.chem.uu.nl/nws/www/publica/e2004-103.pdf,
conventional crystal solar PV uses 15 g SI/wP,
Spheral uses 9 g and Sliver uses 1.5 g. However
the SI used by Spheral may actually be the beads
produced by the fluidized bed system, which avoids
a lot of expensive steps to full ingot. It is
not clear with Sliver what their input source
is or how expensive their manufacturing processes
are, but it looks tricky, whereas spheral is already
in demo volume production with a process they've
been perfecting for 5 to 6 years now.
|
Kevin hagen
11.16.04 |
Murray;
Thanks for your article and research it's
a good view into the future of solar.
While the long term benefits of solar are
interesting at the utility scale, I would argue
that there are many more benefits for PV as
a distributed generation technology. These include
lower installed costs as part of other structures
(e.g. Building integrated PV), reduced or eliminated
transmission losses, and many benefits around
user control. It’s also interesting that
end users are willing to capitalize the generation
investments.
As something of an industry outsider it is
interesting to me that the utility world is
very comfortable with the notation that countless
tiny loads aggregate into huge demand, but somehow
we discount the idea that small sources might
aggregate into part of the solution.
As an example of present market status and
perhaps market trends to come, consider peak
power usage in southern California.
Currently peak retail power cost in many areas
is 32 cents per KW/Hr. PV is routinely being
installed in those areas at $7/Watt (before
rebates, incentives, buy-downs, etc.). In the
simplest calculation, with no incentives, this
cost produces power over a 25 year life at 19.7
cents/KWHr for a 12 cent savings. (see footnotes
for the math)
Before I get 100’s of posts about the
long payback time or oversimplifying the math
in this calculation, let me emphasize that the
point here is to think retail, your customers
do.
I work with corporate and institutional clients
all the time who start with this basis and then
add additional benefits such as hedging electricity
costs and then turn the marketing dept loose
to find some “soft stuff” and come
away with the conclusion that solar PV is a
good deal now.
Kevin Hagen Shuksan Energy www.shuksanenergy.com
Footnote on the math
1 KW DC nameplate of reasonably well installed
PV delivers about .75 KW AC (figure can vary
based on installation, equipment, etc from .7
to .8 and is based on experience and supported
by work at Sandia labs and others for grid connected
batteryless systems in the 5 to 50 KW class).
Southern CA insolation taken at 5.2 solar hours.
.75KW x 5.2 Hrs = 3.9 KWHrs/day. 25 year system
life yields 35,587 KWHrs @ $7,000 = 19.7 cents/KWHr
Of course a real payback analysis is more
sophisticated and would add cost of money, minor
M&O expense, etc. However, it would also
consider direct and indirect incentive programs,
future electric cost increases and other factors.
|
Murray Duffin
11.17.04 |
Len - Thanks a
million for the Alsema reference. I had not seen
it before. He raises a couple of red herrings
unfortunately. By 1999 my employer had phased
out SF6 and reduced PFC use by about 80% with
hopes of eliminating them also. We had also converted
most production to lead free solder, and are probably
past 100% conversion by now. As for health risks,
the entire microelectronics industry has been
using these chemicals in high volume production
for years and years with zero health issues. Sliver
cells not only have 1/6th the Si of spheres, but
will undoubtedly have higher conversion efficiency.
Murray |
Chuck Simmons
11.17.04 |
Kevin --
Nice discussion of the fact that Solar competes
with retail costs, not wholesale.
Murray --
I greatly enjoy your articles. I've been thinking
about the extent to which polysilicon feedstock
supply and prices will impact the rate of growth
of the Solar PV industry. I have basically three
comments:
1) The rule of thumb for the industry appears
to be that polysilicon feedstock usage per watt
drops about 10% per year. Thus, if 17MT/MW were
used in 2000, we would currently use about 11MT/MW.
(Photon magazine reported 13 MT/MW in 2003 which
is inline with this estimate. [Google: photon
13 tons]).
2) Solar module and solar cell manufacturers
are rapidly building new factories. It appears
that in 2005, manufacturing capacities of cells
and modules will be double what they are in
2004. It seems unlikely that so many manufacturers
would expand production if they were not confident
of increased supplies. I also notice that Elkem
is substantially increasing its ability to manufacture
silicon metal, implying that they expect strong
growth in demand; and I speculate that the demand
is coming from polysilicon producers.
3) There is evidence that polysilicon producers
are expanding capacity. USGS estimates 2004
production at 25,000MT. Wacker has been expanding
production and has plans to continue expanding
production. SGS (Solar Grade Silicon) recently
built 2400MT/year of capacity in Moses Lake,
Washington. Tokuyama is addressing bottlenecks
in their production lines to slightly increase
capacity.
So, it looks like the industry, which has
been expecting Solar PV to start driving demand
for polysilicon for years, is prepared to handle
the upcoming increases in demand.
|
David Katz
11.17.04 |
While this article
reflects a wealth of information regarding solar
I would like to add that Daylighting, both active
and passive should also be considered solar energy.
Why take the sun and convert it to electricity
with low efficiencies and then bring it to a ballast
that turns on a light bulb, when you can capture
that sunlight in innovative ways and dim or turn
off the adjacent light fixtures in real time,
usually value peak time, by harvesting the daylight.
Check out www.daylighting.com
|
Murray Duffin
11.18.04 |
Chuck, thanks
for the input. PV would still be limited by poly
capacity and price, but you are suggesting that
the capacity will not severely limit growth and
price might not rise as fast as I suggested. That
is good news. Other - I just came across http://www.nrel.gov/docs/gen/fy04/36831d.pdf.
Page 15 says that at $2.00/Wp installed for solar,
electricity costs only 8 cents/kWh, so I must
have done my calculation way wrong. At $1.80 /Wp
system cost and perhaps $2.00 installed and 8
cents/kWh sliver cells are much more attractive
than I thought, and Roger's caveats become unimportant.
|
Chuck Simmons
11.18.04 |
I did a bit more
reading over the past 24 hours. The main method
by which companies appear to be dealing with the
poly-squeeze is vertical integration. Renewable
Energy Corp (REC) owns a big chunk of Solar Grade
Silicon as well as ScanWafer. This suggests that
ScanWafer will pay a bit more than they want,
and SGS will get a bit less than they want, but
overall, REC will make money. SolarWorld and Wacker
each appear to have similar set ups.
It sounds like Wacker and SGS think that development
of slightly cheaper polysilicon manufacturing
techniques using Fluidized Bed Reactors are
on schedule for volume production in 2006 and
2007.
Meanwhile, the poly producers must be pretty
happy that their factories are starting to run
close to capacity and that they are making money
again. The increased volumes will lower their
costs and raise their profits.
It does sound like cell manufacturers will
need to move to thinner wafers faster than they
might have hoped, but development of equipment
to handle 100 micron wafers has been ongoing
for a few years.
|
Chuck Simmons
11.18.04 |
Just because I
like to play with math, and nitpick... My apologies
for being anal in advance. I want to walk through
some of the math in terms of polysilicon production
and capacity, starting with the paragraph "A&S
estimated that about 2000 MT ...".
I think I found a copy of the referenced article
at "http://www.jxj.com/magsandj/rew/2002_06/silicon_supply.html"
The article suggests that the capacity in
2001 (not 2000) was 26,000 MT, of which 14,000
MT were used, and 12,000 MT unused (not 8,000).
The article does then jump back to the year
2000 and state that 4,000MT were used to produce
235MW of crystalline solar cells. "www.nrel.gov/ncpv_prm/pdfs/papers/57.pdf"
suggests that the remaining MW to reach Maycock's
288MW figure were non-crystalline amorphous
or thin-film silicon and hence didn't consume
an additional 1,000MT of poly. (The PDF uses
a figure of 258MW of crystalline cells. Since
Maycock estimates the 2001 chrystalline market
share at 82%, the 235MW figure seems more consistent
and the 258MW figure looks like a typo.)
In 2003, it appears that 740ish MW of PV were
produced and that about 89% or 660MW were crystalline
for a total solar PV consumption of around 9000MT
of poly. [see "http://www.jxj.com/magsandj/rew/2004_04/pv_market_update.html"
or "http://www.photon-magazine.com/akademie/"].
The USGS estimated overall 2003 polysilicon
production at 23,100MT ["minerals.usgs.gov/minerals/
pubs/commodity/silicon/silicmyb03.pdf"]. So,
there was probably a little bit of excess capacity
(3,000MT) in 2003.
Going way out on a limb... for 2004, solar
companies are reporting 80% increases in revenue,
suggesting that 1300MW of PV are being produced
this year. Assuming 90% crystalline and 11MT/MW,
that's around 13,000MT. The semiconductor industry
consumed 14,000MT in 2003, and probably about
16,000MT in 2004. We can find evidence for the
following capacity additions in 2003/2004: Tokuyama
added 400MT, Wacker added 800MT, SGS added 2000MT
(solar only). These numbers (purely by coincidence:-)
bring both estimated capacity and consumption
to 29,000MT for 2004.
Of course, none of the minor corrections or
additional estimates suggest any changes to
Murray's basic conclusion: either someone needs
to produce a lot more poly in 2005, or the Solar
industry needs to use a lot less silicon in
2005.
|
Murray Duffin
11.19.04 |
Chuck - I do like
people that quantify things, and you found some
sources I didn't, which is all to the good. I'm
glad my tentative conclusion seems to hold up.
Now that poly and crystaline Si people have to
start producing specifically for the PV market
we will probably see some real progress on PV
grade cost and Ein reduction. Murray
|
Todd McKissick
11.19.04 |
Can anyone show me how PV is a better choice
than CSP? I'm looking for an apples to apples
comparison that pits up-front dollars per annual
kWh output. I'm not interested in KW since flat
plate and concentrator systems have different
daily sunlight amounts. I'm also not interested
in how the loan amitorizes out for one when
it's never the same rates used for the other.
Loans are loans and they depend on the buyer's
credit more than any other factor.
I would also be interested in captured area
to grid efficiency to determine land use. The
write-up on Sliver cells quoted 18% but then
added another 75% factor for the ancillary drops.
That drops it down to 13.5% overall efficiency
which is the number that should be compared
to the 23% for Power Towers. I remember Popular
Science promising 30 years ago that we're ready
to make the move from 18% to 31% in PV efficiency
due to some "see through" cells breakthrough.
Still waiting.
What about capacity? You quote that Power
Towers can probably reach 70%. That was simply
the design goal of only the second system ever
built. Any capacity can be attained given a
goal of that number before the plant is built.
This also brings up storage. With no possibility
of storage, PV (and wind) cannot be dispatchable.
This is not the case for CSP. It lends itself
easily to base load as well as peaking.
Then there's O&M. I think the insurance
on PV systems has been missed as an operating
expense. Certainly 10 acres of stowable mirrors
would be cheaper to insure than 10 acres of
expensive fixed mounted PV cells.
With all this talk about the supply of Si
for mfg of PV systems, how about comparing the
energy payback of these two also.
Murray: As to your comment about CSP not needing
any words because "that is already well accepted,
especially for base load", I completely disagree.
The solar thermal direction is only being traversed
by the government labs and very little private
sector development is being done. This is the
sole reason there have been no substantial developments
lately. The DOE's '05 budget finally recognized
it and only added $3M for further study. Let's
see the PV industry get along on that money.
How about wind? Both of these industries are
to the point that with the renewable subsidy
recently passed, they can be self sufficient.
I think that public awareness needs to change
and fast, toward solar thermal systems in order
to ensure that they are not overlooked when
the other two become 'accepted' as the only
ones to make the cut.
PS: I'm not sure why all my earlier paragraphs
got ran together, but there were supposed to
be breaks in there. Sorry for the hard reading.
|
|